“Food is national security. Food is economy. It is employment, energy, history. Food is everything”
José Andrés
Food, one of life’s basic necessities, relies on cold storage for its safe, efficient and effective distribution to U.S. and global populations. The ability to safely deliver food and other temperature-sensitive products from the point of origin to final consumption is a hallmark of a modern and prospering economy; indeed, as José Andrés put forth, food is everything. In aggregate, the various entities and facilities that compose this distribution system are commonly known as the global cold chain, and this chain is widely regarded as a critical component of our economic infrastructure. As we will highlight in this paper, the global cold chain is perhaps one of the most under-invested and under-improved infrastructure sectors in the U.S. and across the globe.
The Food Supply Chain
The U.S. and global economies are in a precarious position, teetering on the edge between a soft landing or recession. While recession typically forces a softening in overall consumer demand and spending, we expect demand for food to remain firm in the coming years, as demand for food is relatively inelastic. In other words, as a basic necessity, demand and spending on food remains strong even during weaker economic conditions. Going forward, we believe that the cold portion of the global supply chain will become increasingly more important as the value added by temperature-controlled storage advances in step with the demand for the products and customers that it serves.
The infrastructure currently in place to support the overall cold storage market has not evolved with the demands of the sector. With the average age of a cold storage building sitting at roughly 40 years old, these older properties generally lack the modern racking and cooling systems necessary, not only for the efficient production and distribution of food, but more importantly for the safe handling of our food supply chain. Against this backdrop, the shortage of modern, cold storage facilities present a prime investment opportunity. By acquiring, renovating, and developing these infrastructures, we can meet the growing demands of food purveyors and consumers. We believe this endeavor could provide attractive risk -adjusted returns for investors. The following paper intends to provide relevant information with respect to the overall cold storage market and the investment opportunity.
What is Cold Storage?
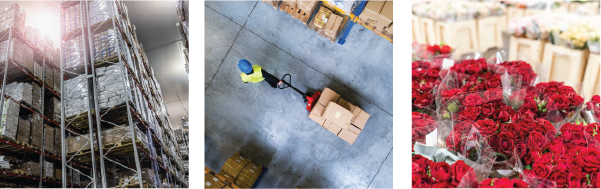
The term “cold storage” typically refers to the segment of the industrial sector that specializes in temperature-controlled spaces, varying from refrigeration to deep freezers and, in some cases, including humidity controls. Cold storage can include buildings that are wholly temperature controlled or offer both dry and temperature-controlled spaces within one building. These properties are used in a variety of capacities from storing food products like meat, dairy, poultry, produce and frozen goods to food production, flowers, pharmaceuticals and other perishables.
In addition to segmentation by temperature, the market is also divided by warehouse type: public versus private. The difference between public and private warehouses is somewhat distinct to cold storage. Public warehouses in cold storage generally refers to warehouses where the owner/operator rents space per pallet to tenants. The owner/operator typically provides handling, packaging and other services to the tenant and distributes products on behalf of the pallet renter/tenant. Americold and Lineage dominate the public warehouse space; Americold (NYSE: COLD) is a publicly traded company while Lineage is owned by a private equity firm, Bay Grove. Lineage is reportedly eyeing a $30 billion IPO in 2024. The public warehouses owned by Americold and Lineage are typically comprised of 100% freezer and located closer to product origination and generally measured in cubic square feet. Private warehouses, in contrast, are leased like traditional warehouses, on a per-square-foot basis, with net leases to third-party tenants. Further, it is common to find various temperature-controlled spaces (including freezer and cooler) as well as dry spaces in one property. Private warehouses also tend to be located closer to the end user (consumer) of the products rather than where the food originated.
Quantifying the Size of the Cold Storage Sector
Cold storage is a relatively small but fast-growing industrial subsector in the U.S. Quantifying the size of the market is challenging, given that 1) a number of properties have a combination of cold and dry spaces; and 2) some dry spaces have been converted or retrofitted to cold or vice versa. The USDA estimates the size of the U.S. cold storage market to be roughly 3.0 billion usable cubic feet as of late 2023, down 1.2% from late 2021. Per the USDA, over half of this space is located in eight states: California (10.3%); Washington (7.8%); Wisconsin (7.6%); Texas (7.0%); Florida (6.2%); Pennsylvania (6.3%); Illinois (4.9%); and Georgia (4.8%). Roughly 80% of the usable cubic feet tracked by the USDA is categorized as freezer space (0-32 degrees F) while the remaining 20% is defined as cooler space (33-39 degrees F). However, the USDA data focuses primarily on commodities, which are cooled to temperatures below 50 degrees F and are stored for 30 days or longer. Given this criteria, the focus of the USDA is generally on the public segment of the market, providing little usable or actionable data on the private segment of the market.
Again, ascertaining the true size of this segment of the market is difficult, given the challenges highlighted above; however, CoStar provides individual property-level data and broader market statistics on the food processing/refrigeration/cold storage market that are useful in assessing the property characteristics and overall market fundamentals. Per CoStar, there are roughly 623.5 million square feet of food processing/refrigeration/cold storage space across the U.S. in nearly 7,000 buildings. Like the USDA data, over half of the square footage in the U.S. is concentrated in eight states: California (17.5%); Texas (7.7%); Illinois (7.2%); Florida (4.8%); Wisconsin (4.4%); Pennsylvania (3.9%); Ohio (3.9%); and Georgia (3.8%). Broadening to the top 15 states, the market share increases to nearly 71% of the cold storage universe. Again, with private warehouse generally being located near the end user/customer/consumer, it is not surprising to see these states are dominant players in terms of cold storage size. Indeed, among the top 15 cold storage states, all but Wisconsin, Massachusetts, Oregon and Minnesota are also among the top 15 most populous states (Figure 1). Metropolitan areas yield few surprises with most areas ranking in the top 15 for population (Figure 2) or being in close proximity to those areas in the top 15 (i.e. Fresno, Stockton and Modesto).
Figure 1: Top 15 States by Cold Storage/Food Production Square Footage with Corresponding Population and Population Rank
Source: CoStar, Moody’s Analytics, as of 2024 Q1
Figure 2: Top 15 Metropolitan Areas by Cold Storage/Food Production Square Footage with Corresponding Population and Population Rank
Source: CoStar, Moody’s Analytics, as of 2024 Q1
Locationally, the inventory of cold storage/food production properties in the top 15 states and markets allows for easy and quick access to 62% and 25% of the U.S. population, respectively. More broadly, this inventory is critical in ensuring the food security for these markets, as well as the U.S. and global populations. That said, the inventory falls short of providing the necessary modern infrastructure required to serve these populations effectively and efficiently. The under-investment in the sector is apparent when delving into the property specifications from CoStar. Roughly 60% of all cold storage/food production properties were built prior to 1990 and nearly 75% were built prior to 2000 (Figure 3). Meanwhile, the average height of properties built before the 1990s is roughly 20 feet, well below the 33-foot average since 2010 (Figure 4).
Figure 3: Cold Storage/Food Production Inventory by Decade Built*
(Data labels are the share of the total 537 msf with a known year built)
*Excludes properties where the year built is unknown
Source: CoStar, as of 2024 Q1
Figure 4: Average and Maximum Ceiling Height of Cold Storage/Food Production Inventory by Decade Built*
*Excludes properties where the year built is unknown
Source: CoStar, as of 2024 Q1
Cold storage-related equipment and controls have improved exponentially over the past ten years per Refrigerated & Frozen Foods1, and the bulk of properties in today’s universe do not offer the advantages of these technological changes. Changes in dock design, dock control systems, cooler and freezer doors, refrigeration controls and equipment software enhancements all allow for a safer employee environment and more reliable food storage and distribution, which in turn yields lower operating costs for tenants. Additionally, newer properties with higher clear heights are better able to use automation. For the past several years, a lack of available labor has been a primary concern among industrial tenants, and cold storage tenants are not immune to this. If anything, they are impacted to a greater degree as finding and retaining potential workers to a cold environment is exceedingly difficult. According to a survey by the Global Cold Chain Alliance, labor turnover in the cold storage industry averaged nearly 33% in 2019, one of the highest rates across all sectors and more than nine times the broader U.S. average turnover (3.6%) in 2019.
Overall, implementing newer building technologies and automation can result in substantial labor and energy savings, the two highest tenant costs (per Lineage Logistics2). However, the inventory that exists today is inadequate to implement these technologies and automation, increasing the need to replace the existing, physically obsolete inventory with new, modern facilities with larger square footage and higher clear heights. Moreover, the investment required to incorporate robotics into warehouses is significant. In fact, in 2017 Walmart began partnering with Symbotic, a robotics and automation company, and recently spent $350 million to automate a warehouse in Cullman, Alabama. Put simply, an investment of this magnitude requires a much different cold storage warehouse than the average warehouse that exists today. To cover the cost of such an investment, the life expectancy of the building needs to be considerably longer than that of the current inventory. In general, the payback on the automation build out is anywhere from 5-10 years, but the useful life of the system is estimated to be 25 years, per Symbotic.
Upgrading the inventory of cold storage buildings will take a significant amount of time as construction activity has been low historically and is expected to remain relatively low going forward. Over the past 24 years, on average only 4.8 million square feet has been completed annually, per CoStar. This is roughly a 1.2% average annual increase in stock, below the 1.6% average annual increase in the broader U.S. industrial market. Moreover, the current pipeline of projects under construction includes less than 11 million square feet, yielding a potential increase in stock of only 1.7%, compared to an under-construction pipeline totaling 2.4% for the broader industrial market. Importantly, the bulk of the cold storage stock that is underway is either build-to-suit product or is 100% pre-leased. Total pre-leasing on the pipeline is 77% compared to 45% for the broader industrial sector.
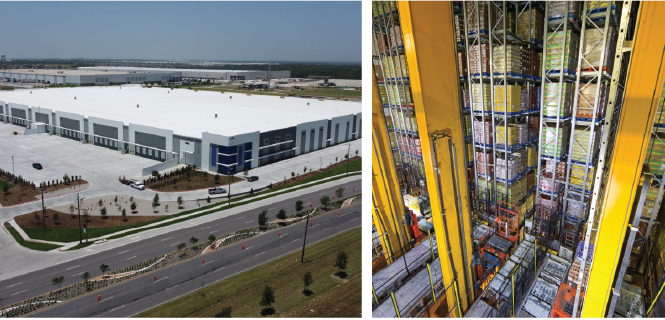
Cold Storage Demand Drivers
Over the next 15 years, Moody’s Analytics forecasts food and drinking establishments will increase at an average annual pace of 4.0%, compared to 2.5% growth at food and beverage stores. On a real basis, average annual sales growth at food and drinking establishments is expected to be 2.3%, outpacing real disposable income growth of 2.1% and the 0.4% growth in sales at food and beverage stores. Combined, the increase in retail sales of both food at home and away from home will be a significant demand driver for cold storage with a real increase in total food sales of roughly $380 billion over the next 15 years (nearly $1.5 trillion on a nominal basis).
Figure 5: American’s Propensity to Dine Out will Continue to Climb
Source: Moody’s Analytics, as of 2024 Q1
The way consumers access food from stores is also changing and creating demand for cold storage. Like many traditional retail categories, apparel, computer and electronics and home furnishings, grocery sales are shifting from in-store purchases to online purchases. Per projections from eMarketer, grocery will become one of the largest e-commerce categories by 2026, accounting for nearly 18% of all online sales. Moreover, nearly 13.7% of the $1.6 trillion in total grocery sales are expected to occur online. Today, most e-grocery sales are fulfilled through stores and this is likely to remain the case; however if rising labor costs and an overall scarcity of labor persists, it may shift some fulfillment to larger, regional warehouses. One example is Kroger’s partnership with Ocada, a software and robotics company. Together, Kroger and Ocada are moving to build out a network of automated fulfillment facilities. Kroger is making the investment to handle the expected increase in online volume and to establish a foothold in regions where they do not have a physical store presence. Kroger estimates automated cold storage facilities could handle the volume of 10 to 12 supermarkets. We expect further consolidation of cold storage facilities as grocers, manufacturers and distributors, incorporate greater automation and more sophisticated technologies that cannot be implemented in older, lower-clear height buildings.
Figure 6: Grocery Will Become the Largest E-Commerce Category by 2026
(% of US e-commerce sales)
Source: EMARKETER5, as of 2024 Q1
Figure 7: Grocery is a Massive Retail Category and Still Has Room to Grow in Online Sales
Source: EMARKETER, as of 2024 Q1
Finally, the last prong of demand for cold storage is through trade. According to the U.S. Department of Commerce’s International Trade Administration, the U.S. imports and exports billions of tons of fresh food products. According to the USDA, U.S. agricultural exports have more than tripled since the late 1990s, increasing from roughly $63 billion in 1997 to $196 billion in 2022. Moreover, the composition of exports has changed with a greater emphasis on cold-chain exports. Exports of high-value products (HVP), which include dairy, meats, fruits and vegetables, have increased at a 5.2% average annual pace since 2008, outpacing the 4.9% growth in bulk exports (grains, oilseeds, cotton and tobacco) over the same period. With the HVP segment of the market, exports of processed and semi-processed food products have outpaced that of raw products. The processed (meat, milk, grain products, processed fruits and vegetables, beverages, essential oils and products of tropical commodities) and semi-processed products (fats, hides, feeds, fiber, flour, meals, oil and sugar) create substantial demand in the cold storage universe, as they use food processing space for production, but also cold storage space for use from production to their port of departure from the U.S., before ultimately arriving at their international destination.
Meanwhile, on the other side of the trade paradigm, growth in food imports, particularly of HVP, has been exponential. Between 1997 and 2022, imports of agricultural products have increased more than five-fold, growing from only $38 billion in 1997 to nearly $200 billion in 2022. As has been the case with exports, since 2008, the growth in semi-processed (9.4%) products has outpaced that of raw products (6.1%) while growth in processed products (6.1%) has matched growth in raw products.
With significant growth in agricultural trade, the need for better cold storage infrastructure is crucial to allow for better access to food, both domestically and globally. Unfortunately, global losses in the food industry total more than 1 billion metric tons, or $750 billion annually. These losses are primarily the result of improper handling and insufficient training in the cold chain. Improving cold chain infrastructure would help eliminate this waste and also keep up with the predicted increase in food trade.
Figure 8: U.S. Exports of Agricultural Products (Billions of USD)
Source: USDA6, as of 2024 Q1
Figure 9: U.S. Exports of High-Value Products by Level of Processing (Billions of USD)
Source: USDA, as of 2024 Q1
Figure 10: U.S. Imports of Agricultural Products (Billions of USD)
Source: USDA, as of 2024 Q1
Figure 11: U.S. Imports of High-Value Products by Level of Processing (Billions of USD)
Source: USDA, as of 2024 Q1
Cold Storage Property and Investment Performance
Given the limited supply growth in the cold storage market and the strength of demand, it is not surprising that cold storage has historically outperformed the broader industrial sector in terms of market fundamentals. Per CoStar, total vacancy within the food processing/cold storage sector stood at 3.1% in 2023 Q4, well below the 5.7% reported for the broader industrial sector. Q4 stood well below the 5.7% vacancy rate reported for the broader industrial sector. Vacancy in the cold storage sector has averaged only 3.6% since 2010 versus a U.S. total industrial average of 6.4% over the same period. At the same time, the volatility in the sector has been considerably lower relative to the overall industrial sector with a standard deviation of 94 bps for cold storage availability, less than half the 201 bps for the broader industrial market since 2010.
Figure 12: Comparative Vacancy Rates
Source: CoStar, as of 2023 Q4
When looking at recently built properties for both cold storage and all industrial, rent growth in the cold storage sector has also outperformed. Per CoStar data, among non-owner-occupied properties built between 2010 and 2022, the overall triple-net asking rent in the cold storage sector has increased at an average annual rate of 13.5%, outpacing the 10.3% average annual increase in the broader industrial sector.
In terms of overall performance, strong rent growth has translated into above-average income growth. Over the past five years, refrigerated storage, as reported by NCREIF, has posted a 4.41% average annual income return, outpacing the broader industrial category and the overall NPI income returns of 4.00% and 4.23%, respectively. The appreciation return for refrigerated storage (7.63%) has far outpaced the broader NPI (0.09%) but was below the broader industrial (10.51%) appreciation return. Overall, the five-year average annual total return in the sector has been exceptionally strong at 14.18%, again outpacing the broader index total return (4.33%) by a significant margin and only slightly below the industrial total return of 14.82%.
Cold Storage Transaction Market
The total transaction volume for cold storage properties has doubled in recent years. From 2019 to 2023, roughly $12.5 billion in cold storage properties changed hands per MSCI Real Capital Analytics, a 32% increase over the $9.5 billion in trades from 2014 to 2018. This, however, pales in comparison to the $647.5 billion in overall industrial trades and the 80% increase in overall transactions over the same time period, again highlighting the under investment in the sector.
At the same time volume has increased, the average price per square foot (psf) of properties that traded has also increased substantially, moving from an average of $83 psf over the 2014 to 2018 period to $129 psf over the 2019 to 2023 period; again, this compares to the broader industrial average increase from $76 psf in the 2014 to 2018 period to $113 psf over the 2019 to 2023 period. Narrowing to the top quartile of cold storage properties traded, and the average trade was $195 psf from 2019 to 2023; however, the psf average in the top quartile eclipsed $200 psf in 9 of the past 20 quarters.
While transaction volume has increased notably over the past five years, the cold storage sector has not been immune to the slowdown in the broader transaction market over the past year. Transactions in 2023 totaled just under $1.4 billion, down roughly 35% from 2022 and nearly half the 2021 volume. Over the past 24 months, the largest acquirers of cold storage properties have been Scout ($290 M); Prologis ($168 M); Pontegadea ($156 M); LBA Realty ($129 M); and Platform Ventures ($119 M), combining to acquire $862 million in property7. Notably absent from the top five buyers list was Bay Grove Capital, the owner of Lineage Logistics. Reportedly, Lineage is looking to go public with a $30 billion IPO potentially in 2024. Going forward, with the debt market easing, we expect transaction volume will steadily increase over the course of the year. We also expect buying opportunities to improve as current owners, who bought at record low cap rates a few years ago, may be forced to sell upon debt maturity due to a potential debt funding gap.
Figure 13: Transaction Volume and Pricing
Source: MSCI RCA 2024 Q1
Prior to the increase in interest rates, cold storage properties, like industrial properties in general, experienced compressing yields (capitalization rates). For cold storage properties specifically, CoStar yields narrowed from over 7% pre-COVID to under 5% in late 2021. Since then, cap rates have generally trended upward, with a 6% average in the second half of 2023. The MSCI RCA Cap Rates are similar to CoStar, while the Green Street REIT Implied Cap Rate and NCREIF cold storage cap rates are generally lower. Overall, historically, the CoStar, Green Street and RCA spread to the overall NCREIF industrial cap rates averaged 225 to 250 bps since late 2017; however, the spread has ranged from over 300 bps at times (pre-COVID) to around 100 bps during COVID and immediately after. Since then, the yield spread has widened once again. Within the NCREIF universe, the yield spread between overall industrial and cold storage cap rates has compressed from over 100 bps in late 2017 to an average of roughly 40 bps today. With solid fundamentals and increased capital flowing to cold storage, we expect the spread to overall industrial cap rates will remain narrow relative to the pre-COVID spread.
Figure 14: Comparative Cap Rates
Sources: NCREIF, MSCI RCA, Green Street and CoStar, as of 2023 Q4
Conclusion
Cold Storage is a relatively small but vital component of the global supply chain, servicing the growing and evolving demand for products requiring various degrees of temperature control. The stock of refrigerated warehouses in the U.S. is relatively old and the higher development cost of building new cold facilities which discouraging speculative development, resulting in slower growth in stock, relative to traditional warehouse spaces. Given the limited and antiquated stock that exists today, waste and inefficiency are pervasive in the market; further, advances in new technologies and automation, which would result in lower costs and greater efficiencies, cannot be implemented in the existing stock of properties today. This presents opportunities to provide tenants with newer, more modern spaces through the renovation or conversion of existing dry space to cold or ground-up development. While obsolescence is a demand driver in and of itself, the cold storage sector’s more traditional demand drivers (demographics, income growth, consumer spending and trade) provide strong long-term tailwinds for the sector as well. As such, we expect the sector will continue to enjoy lower structural vacancies, above-average rent growth and strong NOI growth in the years ahead.
1 Joe Ellestad, Refrigerated and Frozen Foods, “Trends in Cold Storage Equipment and Technology,” Cold Storage Industry News, November 27, 2023, https://www.refrigeratedfrozen....
2 Heather Clancy, GreenBiz, “Why this Cold Storage Warehouse Operator Warmed up to Artificial Intelligence”, Practical Magic, October 10, 2019, https://www.greenbiz.com/artic....
3 Amy Quinton. (2019). Why is one-third of our food wasted worldwide? How stopping food waste can help feed a growing population. https://www.ucdavis.edu/food/n....
4 P.W. Gerbens-Leenes, S. Nonhebel and M.S. Krol. (2010). Food consumption patterns and economic growth. Increasing affluence and the use of natural resources. Appetite, 55(3), 597-608. https://doi.org/10.1016/j.appe...
5 Per EMARKETER, grocery items are products that people regularly buy from a grocery store, including food and beverages, pet food, household cleaning products, personal care products, and other household consumables; excludes restaurant sales.
6 https://www.ers.usda.gov/topic...https://www.ers.usda.gov/topic...
7 MSCI Real Capital Analytics, as of a twenty-four month period ending 4/26/2024.
This material is intended for information purposes only and does not constitute investment advice or a recommendation. The information and opinions contained in the material have been compiled or arrived at based upon information obtained from sources believed to be reliable, but we do not guarantee its accuracy, completeness or fairness. Opinions expressed reflect prevailing market conditions and are subject to change. Neither this material, nor any of its contents, may be used for any purpose without the consent and knowledge of AEW. There is no assurance that any prediction, projection or forecast will be realized.